一、传统公差分析为何成为制造业的“效率黑洞”?
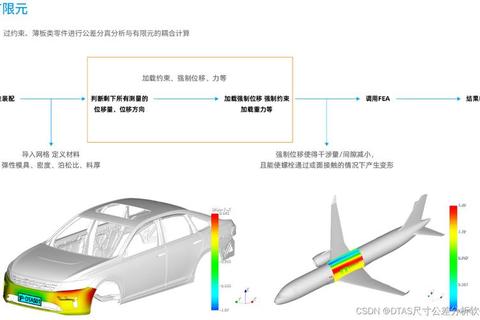
在机械制造领域,一个令人头疼的现象长期存在:设计图纸上每个零件都标注了合理公差,但装配时总出现干涉、异响甚至功能失效。某汽车零部件企业曾因车门密封条装配间隙超差,导致整车厂索赔1200万元,事后追溯发现是6个关联零件的公差叠加所致。这种“纸上完美,实物偏差”的矛盾,正是传统尺寸链计算手工作业的局限——依赖工程师经验估算,耗时长达2-3周的计算周期,却难以覆盖材料形变、温度影响等复杂变量。
智能高效!全面升级尺寸链计算及公差分析软件解决方案的出现,彻底改变了这一局面。重庆诚智鹏科技的DCC软件在某飞机起落架项目中,通过蒙特卡洛仿真法,仅用4小时就完成包含387个尺寸节点的运动误差分析,精准预测了极端工况下连杆机构的失效风险,将试装次数从23次减少到5次。这种将人工经验转化为数字模型的能力,正在破解制造业的“精度魔咒”。
二、国产软件如何突破“三维建模”的技术壁垒?
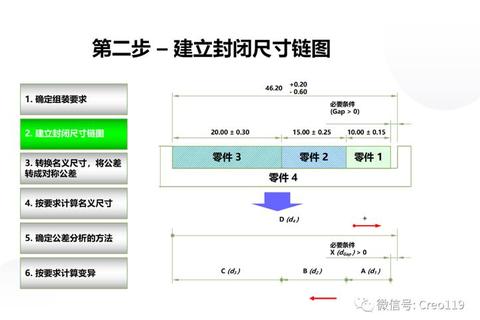
早期公差分析软件停留在二维平面计算阶段,工程师需要对着二维图纸凭空想象三维装配关系。某医疗器械企业设计CT机旋转支架时,因未考虑轴承座圆柱度公差的空间耦合效应,导致样机运行时产生0.15mm振幅,远超0.03mm的医疗安全标准。
智能高效!全面升级尺寸链计算及公差分析软件解决方案通过三维智能建模实现突破。DTAS3D在某新能源汽车电控箱项目中,利用AI自动识别PMI标注信息,将原本需要15天的手工建模缩短至20分钟。软件自动建立265个特征、65个公差参数的三维仿真模型,准确预测了水冷板与电子元件0.7-0.9mm的临界间隙,避免因散热不良引发的系统故障。这种“数模联动”技术,让公差分析从抽象线条升级为可视化的三维动态仿真。
三、智能算法怎样实现“质量杠杆效应”?
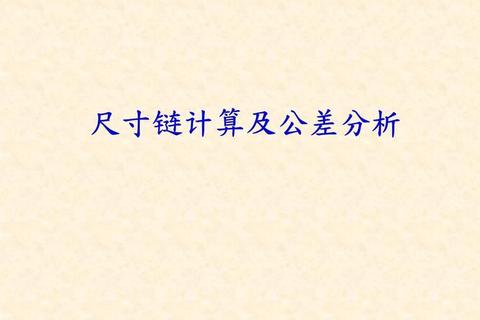
公差优化的核心在于平衡质量与成本。某液压阀制造商曾陷入“精度陷阱”——将零件公差全部提升至IT6级,虽然合格率达到99%,但成本暴涨300%,最终失去订单。
智能高效!全面升级尺寸链计算及公差分析软件解决方案通过大数据+AI的双引擎驱动,创造性地实现精度设计的“性价比革命”。DCC软件在疫苗灌装设备优化中,结合企业历史加工数据,对112个关键尺寸进行公差反演设计。结果令人惊喜:在保持设备运动精度0.02mm的前提下,将高成本公差占比从45%降至18%,单台设备节约制造成本8.7万元。这种基于实际产能的智能公差分配,正是“质量杠杆效应”的最佳诠释——用数据证明:精度提升不一定伴随成本飙升。
破局之道:制造业的精度管理新范式
对于不同规模的企业,落地智能公差分析可分三步走:
1. 诊断痛点:汽车零部件企业可重点突破装配干涉预测,电子企业关注微型化零件的形位公差耦合效应;
2. 阶梯升级:中小企业可从DCC的极值法起步(月成本约3000元),大型企业选择DTAS3D的全生命周期解决方案;
3. 数据沉淀:建立企业专属的“公差知识库”,例如某机床厂积累5年加工数据后,软件自动优化公差的成功率提升至89%。
当某航天发动机企业用三维公差仿真替代了80%的实物试装,当医疗器械厂商凭借智能优化建议拿到FDA认证,这些案例都在印证一个事实:智能高效!全面升级尺寸链计算及公差分析软件解决方案不仅是工具革新,更是中国制造走向“精准智造”的关键一跃。
相关文章:
文章已关闭评论!