现代工程领域的复杂需求正推动设计工具向更高灵活性转型。在智能制造与个性化定制浪潮下,传统CAD软件"大一统"的设计模式已显疲态。某航天装备制造商曾因软件功能冗余导致设计周期延长40%,这个典型案例折射出行业痛点:如何让设计工具既保持专业深度又具备敏捷响应能力?模块化CAD架构的出现,为解决这一矛盾提供了全新思路。
1、架构创新突破
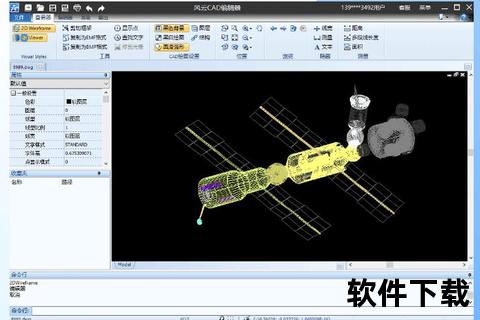
模块化CAD的核心理念在于解构传统软件的"黑箱"结构。通过将几何建模、仿真分析、数据管理等功能拆解为独立模块,工程师可根据项目需求自由组合功能组件。西门子NX平台采用微服务架构后,用户配置效率提升60%,这种架构革新使得软件能够像乐高积木般灵活重组。
底层API接口的开放是模块化落地的关键。达索系统推出的3DEXPERIENCE平台提供超过2000个开发接口,允许企业将专利算法嵌入设计流程。某新能源汽车企业通过接口二次开发,将电池热管理模块与CAD系统深度集成,碰撞测试迭代速度提升3倍。这种开放性打破了软件开发商与使用者之间的技术壁垒。
2、场景适配革命
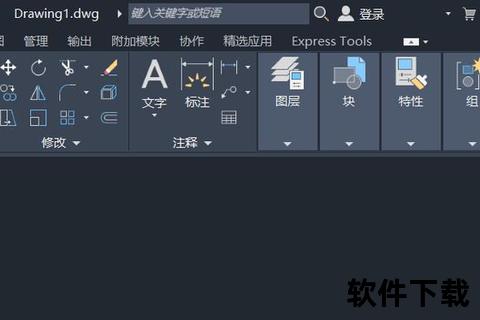
在复杂装备制造领域,模块化优势尤为显著。波音787客机设计过程中,全球30个国家的供应商使用定制化CAD模块协同工作,数据交换效率比传统模式提升75%。每个模块都预置了适航认证标准检查功能,确保分布式设计仍能满足严苛的航空规范。
民用产品设计则展现出另一维度价值。某智能家居企业利用模块化CAD快速搭建卫浴产品参数化模型库,设计师通过拖拽模块即可生成上千种设计方案。市场反馈数据显示,这种敏捷设计模式使新品上市周期缩短至原来的1/3,客户定制需求满足率从58%跃升至92%。
3、用户驱动进化
模块化架构重新定义了软件开发范式。Autodesk推出的Forge平台允许用户投票决定功能模块开发优先级,这种众包模式使软件更新更贴近实际需求。工业设计协会2023年调研显示,采用用户参与式开发的CAD工具,其功能使用率比传统软件高出40%。
知识沉淀机制是持续优化的保障。三一重工将二十年泵车设计经验封装为专用模块,新工程师借助该模块可快速完成80%的标准化设计。这种企业知识资产的数字化封装,使设计效率与质量实现双重飞跃,错误率下降65%的创新方案产出量增加2倍。
4、数据互联新生
模块间的智能连接催生新的工作流。PTC的ThingWorx平台通过物联网模块实时获取设备运行数据,反向驱动CAD模型自动优化。某风电企业应用此技术后,叶片气动外形迭代周期从三个月压缩至两周,发电效率提升8.2%。这种数据闭环彻底改变了传统单向设计模式。
云原生技术拓展了协同边界。欧特克Fusion 360的分布式模块支持200人实时协作设计,版本冲突率降低90%。某国际设计团队利用云端模块化工具,在48小时内完成应急医疗方舱的跨国协同设计,验证了模块化架构在紧急工程中的独特价值。
5、生态演进方向
人工智能正在重构模块化形态。ANSYS Discovery Live引入AI推理模块,能够根据设计意图自动推荐优化方案。麻省理工学院的实验表明,AI辅助模块使复杂结构拓扑优化耗时从数小时缩短至分钟级,材料利用率提高15%-20%。
标准化建设决定发展深度。ISO于2023年发布的模块化CAD接口标准,统一了数据交换协议,使不同平台模块兼容性提升80%。中国工信部牵头制定的智能制造软件互操作规范,正推动形成模块化设计的"中国方案",已有35家装备制造企业通过该标准实现设计系统改造。
当全球制造业面临转型升级压力时,模块化CAD展现出的不仅是技术突破,更是工程思维范式的转变。Gartner预测,到2026年70%的工业软件将采用模块化架构。这种转变要求企业重新审视数字化转型路径:构建可进化的数字工具链,培育模块化设计思维,建立开放的技术生态。未来的竞争,或将取决于企业整合与创造模块化价值的能力。
相关文章:
文章已关闭评论!